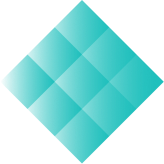
Pilots
The DiMAT Solutions will be demonstrated in 4 pilots representing 4 relevant material manufacturing sectors such as: Polymer, Composite, Glass and Graphite.
The pilots will be implemented to show the applicability and impact of the project and its results into the market environment under real-world conditions.
The case studies will summarise the context and situations before and after the use of DiMAT Solutions, along with an estimate of the improvement in the KPIs.
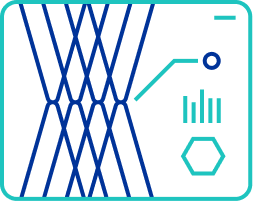
Pilot 1
NATUREPLAST SAS & TECNORED
Synthetic Textiles Production (Polymer)
The pilot will be run by NaturePlast SAS (NTP) which produces renewable plastic compounds with the aim to solve a certain number of issues not resolved by biosourced or biodegradable and unprocessed compostable plastics and Tecnología Redera SL (TECNORED) which manufactures a wide range of fishing nets, construction safety nets, threads and ropes.
DiMAT solutions will support the development of new polymers and other materials in the manufacturing industry. The DiMAT Materials Designer (MD) solution will be used to design new polymers and the DiMAT Materials Processing Simulator (MPS) solution will simulate the production process, allowing cost reduction and improving the generation of new compounds. The simulation will provide a high level of certainty for companies to invest in the development of a new product. The simulation and modelling activities will be further validated with real tests and compared with the results obtained by the DiMAT Materials Mechanical Properties Simulator (MMS). After the simulations, a validation process and material testing will be conducted to verify that the results match the simulation outcomes.
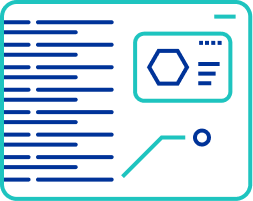
Pilot 2
ACCELI & CETCOMP - UAVs Manufacturing with
Advanced Composite Materials (Composite)
The pilot will be run by Acceligence LTD (ACCELI), Cyprus-based company specializing in cutting-edge R&D activities focused on Unmanned Aerial Vehicles (UAVs), haptics and other robotic solutions and Cetma Composites Srl (CETCOMP), SME that leverages the multiannual expertise of CETMA Research Centre on carbon fibre, thermoplastics and recycling and whose mission includes the production and sale of composite material products for sport, furniture and leisure sectors and also aeronautic sectors.
In this pilot, The DiMAT Suites will be used to investigate the potential use of renewable and recyclable materials for drone structures.
The DiMAT Materials Design Framework (MDF) and DiMAT Materials Modeler (MM) will be employed to design and evaluate these materials. The DiMAT Materials Designer (MD) will analyze requirements and identify the best solution and technology for the sub-components. The DiMAT Digital Twin for Process Control (DTPC) will reduce environmental impact by monitoring key material processes in real-time and optimising them for efficiency. Analytical and numerical models will be utilised to optimise structures and processes. Quality will be determined through a prototyping phase and critical analysis of results, including performance analysis, Life Cycle Cost (LCC) and Life Cycle Assessment (LCA) using the DiMAT Materials Environmental and Cost Life Cycle Assessment (MEC-LCA).
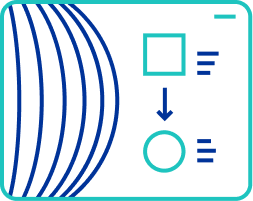
Pilot 3
Hegla-Hanic - Innovative Glass Forming
Process in Digital Environment (Glass))
The pilot will be run by Hegla-Hanic GmbH (HEGLA), German company specializing in the development of digital tools for glass manufacturing processes, with a focus on logistics, ERP and control systems.
The goal of this pilot is to demonstrate how to facilitate digital tools and incorporate data-driven approaches to accelerate the innovative design and implementation of the glass forming process.
The pilot will validate various toolkits including the DiMAT Materials Designer (MD), DiMAT Materials Processing Simulator (MPS), DiMAT Materials Mechanical Properties Simulator (MMS), DiMAT Materials Modeler (MM) and DiMAT Digital Twin for Process Control (DTPC), as well as the DiMAT Cloud Materials Database (CMDB) and DiMAT Knowledge Acquisition Framework (KAF). Key performance indicators (KPIs) will be used to measure the success of the developed solutions, including improvements in data consistency and safety, thermal properties, material design, on-time completion of products, resilience against economic impact and reduction in prototyping procedures.
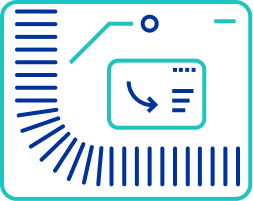
Pilot 4
Imerys Graphite & Carbon - Speeding-up the
New Product Development Process (Graphite)
The pilot will be run by Imerys Graphite & Carbon, Swiss company with a history of delivering high-tech carbon-based solutions to manufacturing and industry, producing synthetic and natural graphite, as well as conductive carbon black for mobile energy applications.
The goal of this pilot is to improve and speed-up the product development process. The pilot will emphasize that process and application development as well as LCA information can be more efficient and affordable.
The pilot will validate the DiMAT Materials Knowledge Acquisition Framework (KAF), The DiMAT Materials Modeler (MM) and DiMAT Materials Designer (MD) for speeding up new product development and reducing the need for physical samples and application tests. The DiMAT Materials Processing Simulator (MPS) will help identify key process parameters on finished product characteristics and suitability for specific applications. The DiMAT Materials Environmental and Cost Life Cycle Assessment (MEC-LCA) will enable new product development managers to accurately consider sustainable impacts throughout the design process.