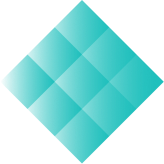
Suites
DiMAT Project will develop 3 solutions called DiMAT Suites.
Each DiMAT Suite will consist of 3 toolkits:
Data and Assessment Suite
– DiDAS
Cloud Materials Database
Knowledge Acquisition Framework
Materials Environmental and Cost Life Life Cycle Assessment
Modelling and Design Suite
– DiMDS
Material Design Framework
Materials
Modeler
Materials
Designer
Simulation and Optimisation Suite
– DiSOS
Materials Mechanical Properties Simulator
Materials Processing Simulator
Digital Twin for Process Control
The DiMAT Data and Assessment Suite - DiDAS
set of digital tools powered by semantic technologies that provide data storage, management and utilization solutions.
The main goal of this suite is to improve the material data safety and material traceability, increase the use of materials from renewable resources and personnel digital skills, reduce material design cost, material economic and environmental impact and time to market.
These set of tools will work together to offer a centralized repository for materials data, enable knowledge acquisition and assess materials based on their environmental impact and cost over their life cycle.
Data and Assessment Suite will consist of:
DiMAT Cloud Materials Database – DiCMDB
system for storing, sharing, and exploration of relevant material data for the material design, processing, and manufacturing processes.
DiMAT Knowledge Acquisition Framework – DiKAF
toolkit for representing and managing information related to the materials along with their characteristics and their relationships in the form of a Knowledge Graph (KG).
DiMAT Materials Environmental and Cost Life Cycle Assessment – DiMEC·LCA
tool for providing a high-level assessment on the environmental and economic impact of the pilot cases.
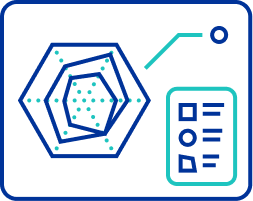
The DiMAT Modelling and Design Suite - DiMDS
set of digital technologies for material design that allows for prediction of material behaviour before manufacturing.
The main goal of this suite is to improve material designs and personnel training ROI, to reduce material design errors and use of material during designing and modelling, to increase personnel productivity.
These set of tools will work together to enable material design in terms of internal structure, properties and performance.
Modelling and Design Suite will consist of:
DiMAT Materials Design Framework – DiMDF
Ontology-based open knowledge system to support the material design process, an App running on DiMAT Open Cloud Materials.
DiMAT Materials Modeler – DiMM
Toolkit to assist in discovering and designing competitive materials rapidly and effectively by modelling.
DiMAT Materials Designer – DiMD
A user-friendly tool for calculating and comparing the mechanical and physical properties of complex materials via virtual testing.
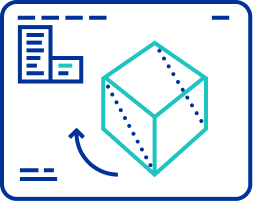
The DiMAT Simulation and Optimization Suite - DiSOS
set of digital tools for material manufacturing simulation and material behaviour prediction.
The main goal of this suite is to improve material mechanical properties and material performance, to increase of on-time completion and material operational characteristics, to reduce material for testing and prototyping procedures and material production cost.
These set of tools will work together to create efficient simulation processes and determine the behaviour of mechanical characterization models for use in AI training and prediction.
The DiMAT Simulation and Optimization Suite will consist of:
DiMAT Materials Mechanical Properties Simulator DiMMS
toolkit for determining numerically mechanical properties such as stiffness, tensile strength, plasticity, viscoelastic and viscoplastic properties, damage, fracture, fatigue, etc.
DiMAT Materials Processing Simulator DiMPS
toolkit for determining manufacturing conditions and concepts while simulating their application, results and requirements, in each one of the materials, processes, and processing conditions found at the DiMAT Open Cloud Materials Database.
DiMAT Digital Twin for Process Control DiDTPC
digital counterpart of the IoT devices considered within DiMAT that provides a set of abstractions, virtualized functions, and APIs to support real and simulated manufacturing processes.
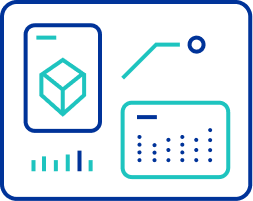